BY STEVE CLARK, TREVOR CARTER AND BRUCE COWELL, EDITED BY PAM CARTER
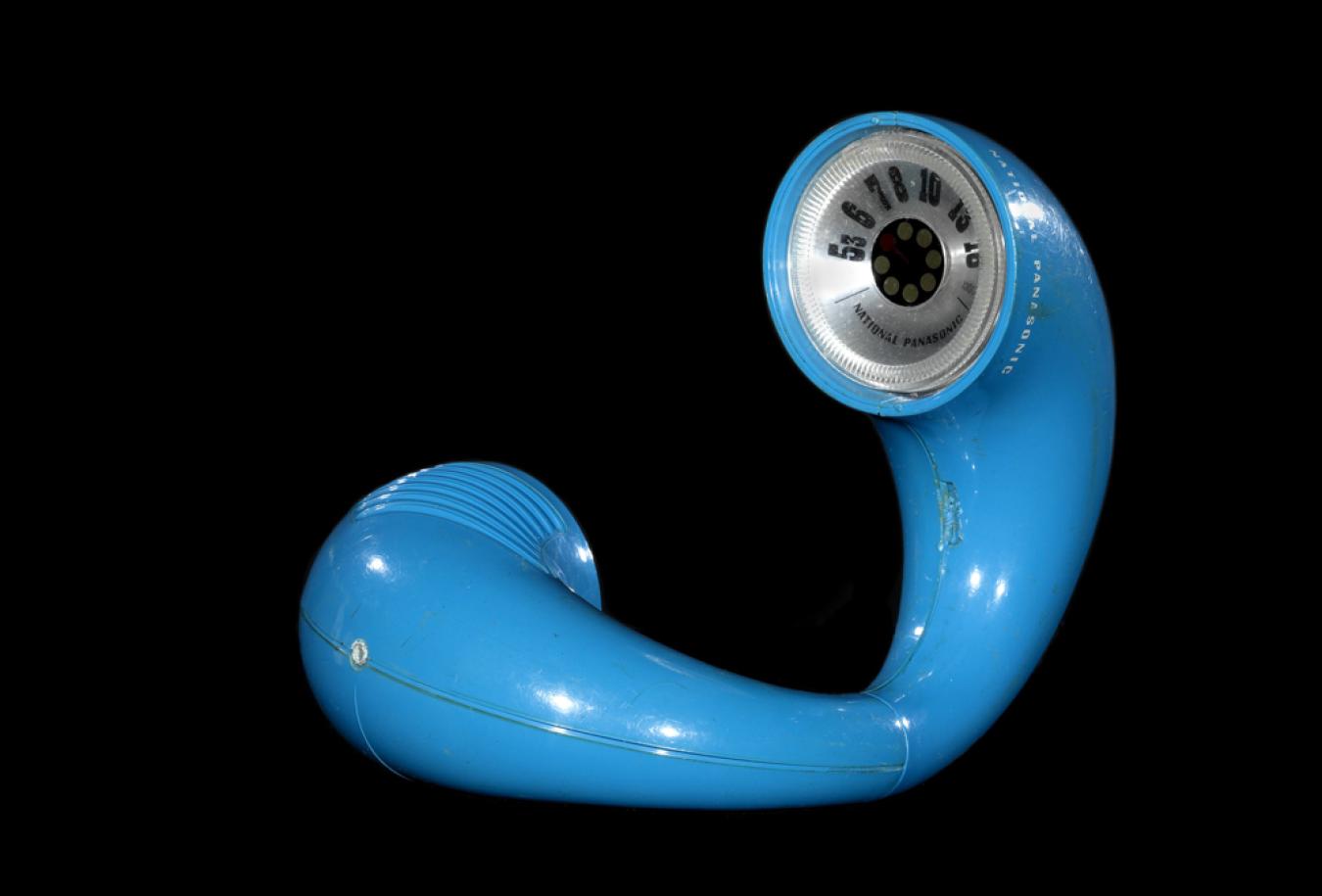
BY STEVE CLARK, TREVOR CARTER AND BRUCE COWELL, EDITED BY PAM CARTER
This is the second in a three-part series. Read Part One and Part Three.
The NFSA’s collection includes early coloured films, many of which are tinted. As these films deteriorate with age, their colours are lost.
Steve Clark, Trevor Carter and Bruce Cowell from the NFSA’s Motion Picture Laboratory share their research about using traditional dyes and techniques to restore tinted films.
The NFSA has been aware of the problems associated with tinted film for many years. In the 1990s, we carried out tinting experiments using liquid food dyes. These dyes were chosen because in-house research found that the main colouring agents in food dyes were based on the coloured aniline dyes used in the original film tinting era. As we will discuss later, this research did not pan out and the pressure of other work led to the experiments being shelved.
In 2007, the NFSA began a targeted restoration program for films in the iconic Corrick Collection. This program is still ongoing and the some of the restored films have been progressively relaunched at the annual Pordenone silent film festival (Le Giornate del Cinema Muto) in Italy. Black-and-white copies of the Corrick films are produced in-house. However, copies of coloured films have had to be created in partnership with external providers with access to specialised equipment (such as film scanners and the Desmet system).
In March 2008, the Motion Picture Laboratory was visited by the renowned audiovisual archivist, Paul Read (co-author of Restoration of Motion Picture Film, 2000, cited in the Endnotes). Read gave a talk on the tinting and toning of early films and discussed work he had carried out in identifying the modern equivalents of original powdered aniline dyes. This talk, and the preservation work required for the Corrick Collection, renewed staff interest in finding ways to reproduce coloured films in-house and the NFSA’s tinting research was reactivated.
As a starting point, Neil Richards and Trevor Carter were asked to reproduce a tinted title sequence for the 1907 short film The Bashful Mr Brown from the Corrick Collection.15 Inspired by Paul Read’s work, we decided to try and source a small quantity of powdered aniline dye. As well as using liquid food dyes, an attempt would be made to reproduce formulas and methods from the 1920s (found in Kodak manuals on tinting and toning motion picture film).16
The film Bashful Mr Brown is historically important as it was produced by Leonard Corrick and various members of the Corrick family appear in the film. As only the film’s opening title was tinted, we thought that the film would provide a relatively simple start for our reactivated tinting research. As things turned out, the process was not as simple as we had hoped. The black-and-white story part of the film had survived intact; however, only a single frame from the film’s original title sequence still existed. This frame showed that the title had originally been tinted orange. Before we could begin testing the dyes, a new black-and white negative had to be created of the title sequence.
A motion picture is a sequence of still images (known as frames) which, when played back at speed, appears to be a moving image. Films from the silent era were generally shot at a range of 12 to 18 frames per second. Bashful Mr Brown was filmed at 16 frames per second, meaning that one frame of title would appear on screen for only one sixteenth of a second. To create the new title, the original frame needed to be copied multiple times (to allow it to remain on screen long enough to be read). A general rule of thumb when creating titles is that the image should stay up on screen for one second for each word in the title. As the film had a three word title, its single frame was copied and made into a sequence of 48 frames (three seconds at 16 frames per second). This expanded the single frame to a film approximately three feet (one metre) long. The black-and-white negative was then used to produce new cinema positive prints ready for tinting.
Liquid food dyes were purchased from the Aeroplane Jelly Company. An orange tint was produced by mixing Aeroplane Egg Yellow food dye with Aeroplane Red. Aeroplane Egg Yellow contains two original aniline dye colours: Tartrazine Yellow E102 and Sunset Yellow E110. Aeroplane Red contains one aniline dye, Amaranth E123, which is reddish-brown in colour. We had trouble sourcing an orange-coloured powdered aniline dye to compare with the food dyes. Some dyes were no longer in production — others were unable to be used due to health and safety reasons. One dye contained uranium oxide and the importation and use of a uranium-based product was not considered advisable. Eventually, a small quantity of a red powdered dye, Ponceau 2R, was sourced from a scientific supply company (Crown Scientific).
Because the title was made up of 48 frames of moving image, it was roughly equal to 36 frames of still image film. This made it possible to dye the title section using equipment normally used for hand-developing rolls of photographic film. To make it easier to establish a methodology, we started with the material that we had previous experience with: the liquid food dyes. The first step was to figure out the best method to achieve an orange tint with an appropriate depth and hue when compared to the original. We produced a number of clear strips of film (roughly 15 cm long) and tried different concentrations and quantities of dye, testing and recording the formulas used.
We poured 200 ml of water into a 500 ml container, added the dyes, and then added more water to bring the solution up to 250 ml. Each strip of film was dipped for three to five minutes and the dye concentration and time used was recorded. The test strips were washed in running water for no longer than two minutes because the liquid food dyes washed out too much if the film was cleaned for longer. Once each strip had dried it was compared to the original frame by placing the copy and the original on a light box and comparing them by eye. Testing showed that mixing the liquid food colours at a rate of 6 ml of Aeroplane Egg Yellow to 1 ml of Aeroplane Red gave the best match for the orange in the original tinted frame.
Having established the formula, a one litre solution of dye was prepared for tinting the title. At three feet (one metre) long, hand dipping the film was impractical and could have led to an uneven take-up of the dye. Instead, the film was wound onto a photographic frame called a spiral (used in still photography to allow solutions to flow evenly around film). To ensure the dye nearest the film did not become exhausted, which would have resulted in patchy colour, the spiral was agitated through the dye solution (moved up and down by hand).
After tinting, it was crucial that the film dried evenly. It was rinsed in water for two minutes and then rinsed in Kodak Photo-Flo 200 (a detergent used to promote the even drying of film). The film was removed from the spiral and hung in a drying cabinet. When dry, we compared its colour to the original frame and checked that the copy had dried evenly (making sure that there were no water marks and that the colour was even across the film). Once the film passed all these tests it was joined on to a copy of the image section of the film, ready for projection. Two copies of Bashful Mr Brown were produced using this liquid food dye formula. One was kept as an access copy that could sent out for screenings, the other was held at the NFSA in case of damage to the access print.
As part of the Bashful Mr Brown project we ran a side-by-side tinting test for the film, using a powdered aniline dye. It was hoped that, by using an original powdered dye, we would be able achieve a closer approximation of the historic process. However, our first attempt to source powdered aniline dyes ran into problems. Many of the original dyes are no longer produced and the ones that are still available are mostly used in large-scale production in the clothing industry and scientific laboratories. Finding a supplier willing to sell small quartiles (less than a tonne) proved difficult.
Eventually, we were able to purchase a small quantity (50 grams) of a red aniline dye in powder form — Ponceau 2R (xylidine ponceau) — from a scientific supply company (Crown Scientific). Ponceau 2R is an aniline dye listed as producing a scarlet (orange) red colour. The supplier was unable to provide a more exact description of the colour the dye produced. Since we could buy the dye in small amounts, we decided to take a punt and ordered 50 grams of dye. Unfortunately, the colour produced by this dye was not appropriate for the film we were trying to match at the time. Bashful Mr Brown required an orange tint and our initial colour tests showed that Ponceau 2R produced a tint more red than orange-red.
As we had the dye, we decided to continue testing to see what using a traditional powdered aniline dye was like. We used the same hand-developing equipment as we had for the liquid food dye tests; a small quantity of the powdered dye was dissolved in 200 ml of water and the solution diluted by topping up with water to 500 ml. We dyed several short lengths of clear film and the results were very encouraging. The powdered dye produced a clear stable red tint and the times and concentrations of dye used closely matched the historic process as shown in the 1920s Kodak manuals (the primary guides used for this experiment).17
The food dyes used for tinting experiments at the NFSA were chosen because their principal colouring agents are aniline dyes (many of which were used in the original tinting processes during the early years of motion picture film). Using liquid food dyes produced a tinted film close to the colour of the surviving frame as it is now. It did not necessarily give a true indication of what the colour looked like when it was created (we may have matched a faded colour rather that the colour of the original material).
It was hard to judge in what concentration to use the dyes to reproduce the historic colours. Liquid food dyes contain aniline dyes mixed with other ingredients (water, citric acid and acetic acid) and could not be used to re-create the original dye formulas. In addition, the dye did not reach saturation quickly and the film kept getting darker the longer it was left immersed. This meant that the depth of colour required had to be judged by eye (repeatedly taking the film out of dye solution to look at it and re-immersing it until we thought the correct colour had been reached). This made using these dyes impractical for tinting anything other than short lengths of film.
Liquid food dyes also proved to be chemically unstable and did not bind well with the emulsion. The films could not withstand a long washing time without fading (dye started washing out after only two minutes). An examination of films previously copied at the NFSA showed that copies tinted using liquid food dyes have already decayed to the point where they are no longer usable.
In comparison, the solution containing powdered aniline dye was much more stable. It bound well with the film’s emulsion and could be washed till all the surface dye had been removed. This made it easier to handle and meant that results were reproducible. The take-up of colour was also more consistent: the dye reached saturation point after ten minutes. The colour could be determined based on the concentration of dye used (less dye gave a lighter hue) and it was not necessary to constantly check the film visually. This opened up the possibility of scaling up to machine production, which would allow us to tint much longer sections of film.
In 2009–10, based on the promising results obtained in the testing of powdered aniline dye for Bashful Mr Brown, the NFSA decided to look at the feasibility of scaling up from hand-tinting to tinting using machine methods. The film chosen for the project was a newsreel from 1906: CHAMPIONSHIP BOXING CONTEST: SQUIRES VERSUS KLING. ASCOT RACECOURSE, MELBOURNE (NFSA imposed title).18 This film is thought to be the first footage taken of a boxing match in Australia.
Championship Boxing Contest contains black-and-white action scenes with an orange tinted title and intertitles. As with Bashful Mr Brown, the titles in this film had been damaged and additional text frames had to be created to allow the words to remain on screen long enough to be read. Stretch printing the titles produced approximately 300 feet (91.5 metres) of film — a good length to test machine tinting techniques. Further research found that powdered aniline dyes are still used for staining wood and leather products. We found a Sydney-based company (Wood Works Book and Tool Co.) that would sell us small quantities of powdered aniline dyes (they also had a website that showed the colours produced by the dyes).19 The aniline dye purchased for the Championship Boxing Contest project was called Basic Orange (this colour has since been discontinued).
If the NFSA was to move up to tinting full-length films, machine processing would have to be used. Continuous processing machines provide the most efficient way of handling long lengths of film. The Motion Picture Lab has a spare film processing machine (left over after a machinery upgrade in the 1990s) and we were able to modify this processor for the project. Our earlier tests showed that powdered aniline dye solutions worked best when kept at a temperature of around 20°C and machine processing would allow us to control the temperature and agitation of the dye solution.
With a capacity of 250 litres, the processor’s developing tank was too large to be used as a dye bath and had to be bypassed. We used the (smaller) fixer tank for the dyeing process. The film then went through three wash tanks before ending up in the drying cabinet. By reducing the size and number of tanks, we reduced the amount of dye required to 120 litres (making the process more cost effective). Another benefit of reducing the number of tanks was that it kept the wash time shorter (10-20 minutes), which removed the excess dye without reducing the overall colour.
The film was over 100 years old and its colour had faded. Rather than try to re-create this faded colour we decided to use an original dye recipe. After some research, we used a dye concentration listed in a Kodak film tinting manual from 1927: 1 gram of powdered aniline dye per litre of water. However, hand testing showed that this concentration produced a test strip that was slightly too dark, which would make the titles difficult to read. After more testing, we settled on a formula of 0.6 grams Basic Orange per litre of water.
We now had a concentration that achieved the colour we wanted but the tint was not being taken up evenly across the emulsion. The perforated edges of the film were allowing the dye to penetrate the emulsion layer too easily and the dye was being absorbed much faster at the edges of the film. This meant that the centre of the film was taking up less dye, making it paler in colour. We tried to overcome this unevenness by softening the emulsion layer (soaking the film in a warm, slightly alkaline, solution) prior to dyeing. It was hoped that this would swell the emulsion, allowing the film to evenly absorb the dye — it didn’t work. Eventually, we found we could minimise the effect by agitating the dye solution and keeping the temperate above 20°C. The paler uptake of colour in the middle of the film was minimised and was not visible when projected.
The fixer tank we were planning to use for tinting the film had both a heating element and an agitation pump. If our theory was correct, when the film exited the drying cabinet we would have an evenly tinted film. We mixed 120 litres of dye and went ahead with full-scale production. Our first test using the processor showed a far more even tint than we had hoped for. There was no measurable colour difference between the edges and the centre of the film and the colour held fast through 15 minutes of wash time. Given this result, we went ahead: dyeing 300 feet of title and intertitles and joining them back to the black-and-white image portions of the film. We had successfully created a tinted copy of Championship Boxing Contest using a traditional powdered aniline dye formula and machine processing. This project was a turning point in our research that we would use to inform future preservation work for tinted films.
This is Part Two in a three-part series. Read Part One and Part Three.
15The Bashful Mr Brown (Leonard Corrick, 1909) NFSA Title No. 747585
16Kodak, 1922, Tinting and Toning of Eastman Positive Motion Picture Film (3rd edition), Eastman Kodak Co. [Note: This is a reproduction from a photocopy of the original text and page numbers have not been included]; Kodak, 1927, Tinting and Toning of Eastman Positive Motion Picture Film, Eastman Kodak Co., published online at http://www.brianpritchard.com/Tinting.htm
17Kodak, 1922; Kodak 1927
18CHAMPIONSHIP BOXING CONTEST: SQUIRES VERSUS KLING. ASCOT RACECOURSE, MELBOURNE] (Johnson & Gibson, 1906) NFSA title No.: 7122
19The Wood Works Book and Tool Co., http://www.thewoodworks.com.au/, accessed October 2011
The title for this work was inspired by the Dylan Thomas poem ‘Do not go gentle into that good night’, Dylan Thomas, Collected Poems 1934–1952.
Main photo: Still image from the film Bashful Mr Brown (1907).
The National Film and Sound Archive of Australia acknowledges Australia’s Aboriginal and Torres Strait Islander peoples as the Traditional Custodians of the land on which we work and live and gives respect to their Elders both past and present.